A PO number (Purchase Order number) is a simple but crucial part of business transactions. It’s a unique code assigned to a purchase order, helping buyers and suppliers track orders, process payments, and avoid confusion. Think of it like a receipt number for your business purchases—without it, tracking down an order or resolving a billing error becomes messy and time-consuming.
For example, if a delivery arrives with the wrong items, a PO number lets you quickly reference the original agreement to fix the issue. Whether you’re a small business or a large company, using PO numbers ensures clarity, reduces errors, and keeps finances organized. In this guide, we’ll explain how PO numbers work, why they matter, and how to set up a system that works for you.
What does po number or purchase number mean
A PO number (short for Purchase Order number) is a unique code assigned to a purchase order, which is a document a buyer sends to a supplier to officially request goods or services. It acts like a tracking ID for the transaction, helping both parties reference the order’s details at every stage—from approval to delivery and payment.
For example, a small business ordering 50 laptops from a vendor might issue a purchase order with a PO number like PO-2024-075. Here’s how that number breaks down:
- PO: Indicates it’s a purchase order.
- 2024: The year the order was placed.
- 075: A sequential number to distinguish it from other orders that year.
This simple identifier ensures everyone involved can quickly pull up the agreed-upon terms, such as item descriptions, quantities, prices, and delivery dates. Think of it as a “paper trail passport” that follows the transaction through procurement, fulfillment, and accounting. Without a PO number, tracking orders or resolving disputes (e.g., incorrect shipments or billing errors) becomes a guessing game.
PO numbers ensure clarity, whether handwritten on a form or auto-generated by software. They are the glue that holds organized purchasing processes together.
Where to include po number in an invoice
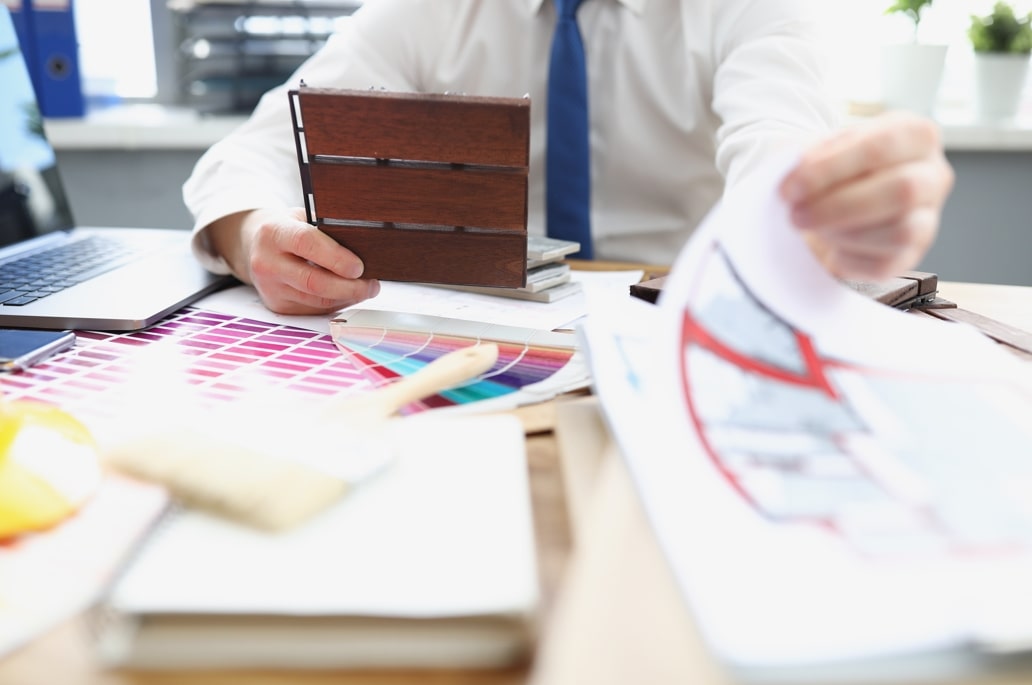
It’s a common practice to include po numbers in a purchase order. It’s not mandatory, but smoothes payment processing and reconciliation for the business. Here’s where to place it:
- Invoice header: Near the buyer/seller details or invoice number (e.g., “PO: PO-2024-075”).
- Payment instructions section: Alongside payment terms or due dates.
- Line item descriptions: Optional, but useful for large orders with multiple POs.
Most businesses prioritize placing the PO number in the header for immediate visibility. For example:
- Invoice #: INV-1016
- PO #: PO-2024-075
- Date: 15 May 2024
This avoids delays—accounts payable teams can instantly match the invoice to the original purchase order.
PO number vs. Invoice number
While both are unique identifiers, they serve different purposes:
PO number | Invoice number |
Issued by the buyer when placing an order. | Issued by the seller when billing for goods/services. |
Tracks the procurement process (approval, fulfillment). | Tracks the payment process (amount owed, due date). |
Key Takeaway: The PO number governs what was ordered, while the invoice number governs what is owed. For instance:
- A buyer sends PO-2024-075 to order 50 laptops.
- The seller delivers the laptops and issues invoice INV-1016 referencing PO-2024-075.
- The buyer’s finance team verifies the invoice against the PO before paying.
Mixing these up can lead to payment delays or mismatched records. Always keep both numbers distinct but linked.
See SMO in action
Try our solutions with zero commitment
How to create a manual PO number system
A manual PO number system relies on simple, consistent formatting and a centralized log to track orders without specialized software. It’s ideal for small businesses or those with low purchase order volumes. Here’s how to set one up:
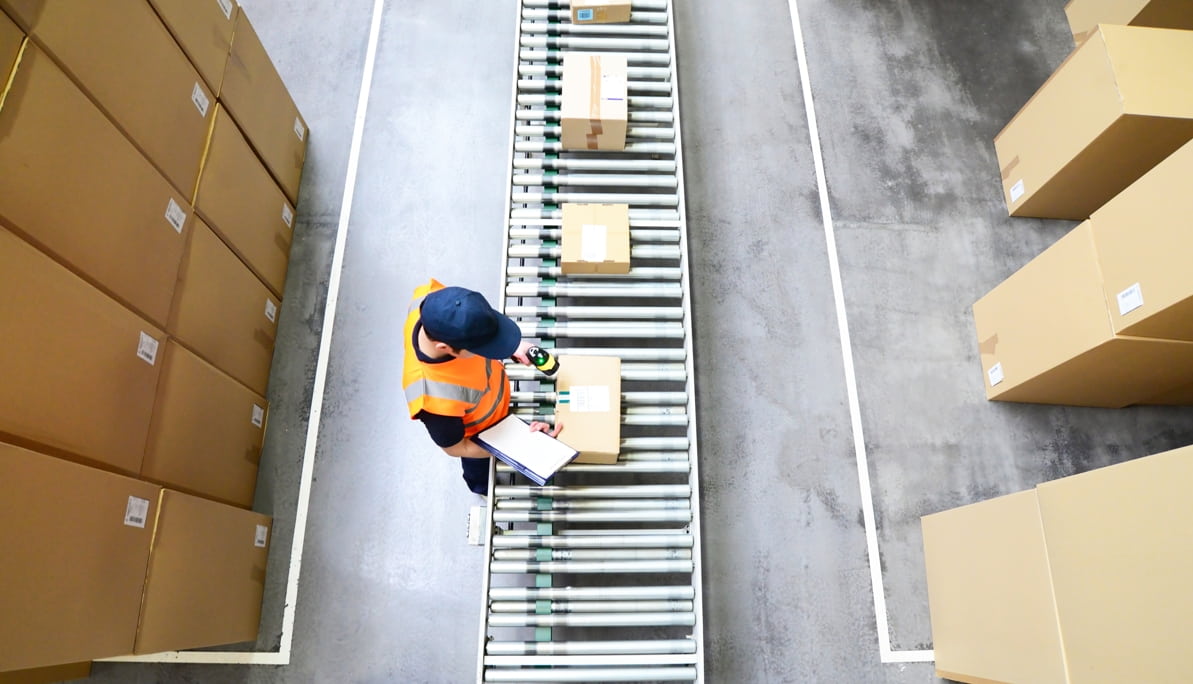
Step 1: Define your PO number format
Keep it short and avoid overly complex codes. Simplicity reduces errors.
Step 2: Use a physical logbook or spreadsheet
Manually track every PO number issued using:
- A bound logbook: Physically write each PO number, date, supplier name, and order details.
- A spreadsheet: Create columns for:
PO Number | Date Issued | Supplier | Order Details | Status (Open/Closed) |
PO-2024-001 | 01/05/2024 | Office Supply Co. | 10 desks, 20 chairs | Closed |
Update this log immediately after issuing a PO.
Step 3: Train your team
- Ensure everyone involved in procurement understands:
- How to assign new PO numbers (e.g., always increment sequentially).
- Where to record them (logbook or spreadsheet).
- Why consistency matters (avoids duplicate numbers or skipped sequences).
Tips to avoid common pitfalls
- Never skip numbers: Gaps create confusion during audits.
- Label revisions clearly: For amended orders, add a suffix (e.g., PO-2024-001-A).
- Archive old logs: Store previous years’ records for reference.
Pros and cons of a manual system
- Pros: Low cost, easy to implement, no software required.
- Cons: Prone to human error, time-consuming at scale, harder to search or audit.
Manual systems work best for startups or businesses with under 50 orders per month. Beyond that, automation becomes essential.
How to create an automatic PO number system
An automatic PO number system uses software to generate, track, and manage purchase orders, eliminating manual data entry and reducing errors. This method is ideal for medium to large businesses or those handling frequent or complex orders. Here’s how to implement it:
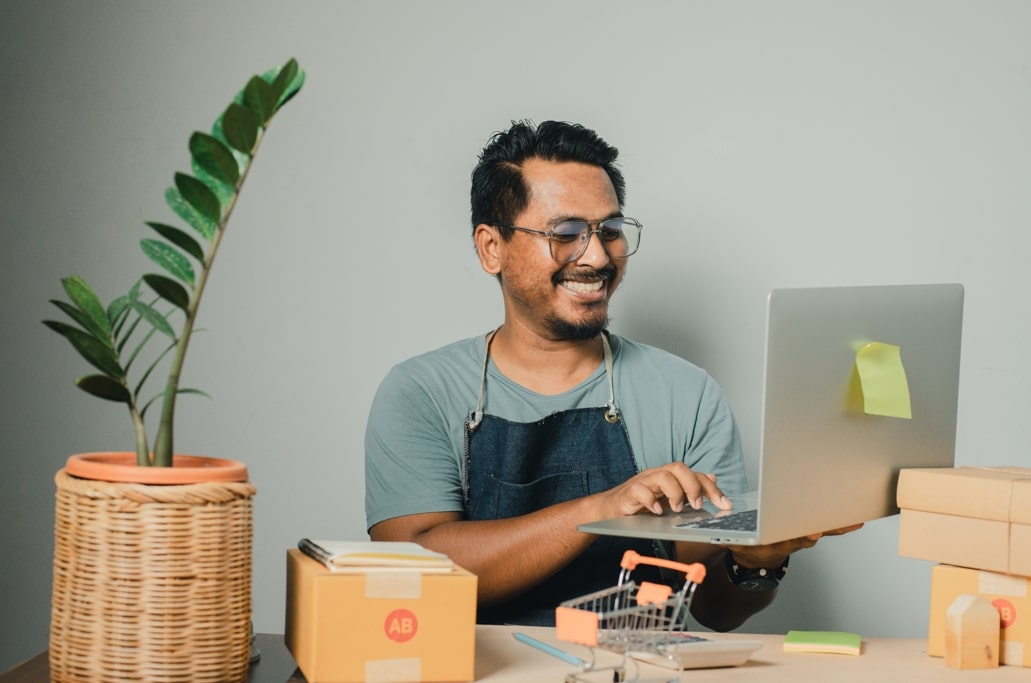
Step 1: Choose procurement software
Select a tool that supports automated PO numbering and integrates with your existing workflows. Options include:
- ERP systems (e.g., SAP, Oracle NetSuite).
- Procurement platforms (e.g., Procurify, Coupa).
- Accounting software (e.g., QuickBooks Online, Xero).
Ensure the software allows customization of PO number formats and automates sequential numbering.
Step 2: Configure your PO number format
Most tools let you predefine a structure. Use placeholders like:
- Prefix: PO, PUR, or department codes (e.g., IT-PO).
- Date: Automatically pull the year or month (YYYY, MMYYYY).
- Sequential numbers: Auto-increment (e.g., 001, 002).
Example:
A company using Zoho Inventory might set a format like PO-{{YYYY}}-{{######}}, generating PO-2024-000045.
Step 3: Set up automated workflows
Leverage the software’s features to streamline procurement:
- Two-way sync: Link POs to inventory management or accounting modules.
- Approval chains: Automate routing to managers based on order value or department.
- Notifications: Alert suppliers and stakeholders when a PO is issued or modified.
Example:
A construction firm sets up an automated approval rule: POs over $5,000 require a project manager’s sign-off before being sent to suppliers.
Step 4: Implement data security and access controls
Restrict permissions to maintain accountability:
- Role-based access: Only procurement staff can create POs; finance teams can view but not edit.
- Audit logs: Track who generated, modified, or approved each PO.
- Backups: Use cloud storage or auto-sync to prevent data loss.
Step 5: Train your team
Ensure staff understand:
- How to generate POs with the new system.
- How to reference or search past POs (e.g., using filters for suppliers or dates).
- Basic troubleshooting (e.g., handling duplicate numbers or software glitches).
Pros and cons of an automatic system
- Pros:
- Reduced human error and faster processing.
- Real-time tracking and reporting.
- Scales effortlessly with business growth.
- Cons:
- Higher upfront cost and setup time.
- Dependent on software uptime and IT support.
Start with a hybrid approach if transitioning from manual. Use software for high-volume orders and manual logs for occasional purchases, then phase out manual processes entirely.
See SMO in action
Try our solutions with zero commitment
Streamline your procurement with PO numbers
PO numbers are more than just arbitrary codes—they’re the backbone of organized purchasing, bridging the gap between order requests, deliveries, and payments. Whether you’re a small business using a handwritten log or a growing enterprise leveraging automation, a clear PO system ensures accuracy, accountability, and audit-ready records.
Key takeaways:
- Consistency is king: Stick to a simple format (e.g., PO-YYYY-001) and train your team to follow it.
- Manual vs. automated: Choose based on your order volume and complexity. Start simple, but scale with tools as needed.
- Prioritize transparency: Ensure suppliers include PO numbers on invoices, and archive records for compliance.
By adopting a PO number system tailored to your workflow, you’ll minimize errors, speed up payments, and build trust with suppliers. Ready to upgrade? Audit your current process today—your future self (and your accountant) will thank you.
Need help setting up a PO system? Collaborate with your finance team or explore procurement software trials to find the right fit.